Recognizing the Principles of Pipeline Welding Examination: Important Elements for Evaluating Weld High Quality and Averting Failings
In the realm of pipe welding evaluation, the stakes are unquestionably high, requiring a detailed understanding of essential concepts to ensure weld quality and alleviate failure dangers. Numerous crucial variables come into play, including the choice of ideal products, the application of sophisticated examination techniques, and the recognition of common welding defects.
Significance of Weld Top Quality
The honesty of a pipeline is fundamentally dependent on the quality of its welds, making weld quality an essential consider guaranteeing risk-free and effective operation. A pipeline weld acts as a junction point where materials are joined, and any type of shortages in this area can result in considerable structural weaknesses. Poor weld high quality can lead to leakages, tears, and tragic failings, presenting severe safety and security threats and ecological dangers.
A number of aspects add to the high quality of a weld, including the choice of welding procedure, the abilities of the welder, and the problems under which the welding is done - Pipeline Welding Inspection. Insufficient preparation, incorrect warm input, and contamination can jeopardize weld stability, bring about concerns such as porosity, insufficient combination, or cracks. Therefore, stringent quality control measures have to be carried out throughout the welding procedure to minimize these dangers
Additionally, the lasting performance of a pipe is heavily influenced by the durability of its welds. High-grade welds not just enhance the total stamina of the pipeline but additionally prolong its solution life, decreasing the need for pricey repair work and downtime. Hence, making certain exceptional weld quality is vital in pipeline layout and maintenance techniques.
Secret Examination Methods
Ensuring weld top quality requires the execution of efficient inspection methods to identify prospective flaws prior to they result in failings. Pipeline Welding Inspection. Among the most commonly made use of methods are aesthetic examination, radiographic testing (RT), ultrasonic screening (UT), and magnetic particle testing (MT) Each method is and serves a distinctive function picked based on the certain requirements of the pipeline task
Visual assessment is the first line of defense, permitting examiners to analyze surface conditions, positioning, and overall workmanship. It is a cost-effective and quick technique that can expose noticeable defects. Radiographic testing gives a detailed view of internal weld stability by utilizing X-rays or gamma rays to identify subsurface flaws. This technique is particularly efficient for determining incorporations, splits, and gaps.
Ultrasonic testing employs high-frequency sound waves to evaluate the density and integrity of welds, making it perfect for spotting inner discontinuities. Magnetic particle screening is a trusted approach for determining surface and near-surface issues on ferromagnetic products by applying magnetic fields and fine ferrous fragments. By using these essential inspection strategies, pipeline welding inspectors can make certain the best criteria are preserved, ultimately bring about much safer and more trusted pipe systems.
Usual Welding Flaws
Amongst the most common issues are porosity, which happens when gas allures in the weld steel, creating spaces that deteriorate the joint. An additional significant problem is absence of blend, where the weld steel does not adequately bond with the base material, jeopardizing the joint's toughness.

Fractures are likewise an important problem, manifesting in various types such as warm splits, cold cracks, and root splits. Each kind poses one-of-a-kind obstacles and requires specific inspection techniques for detection. Undercut is another defect that can decrease the weld's cross-sectional area, leading to tension concentration points, while slag inclusion takes place when non-metallic product comes to be entraped in the weld swimming pool, negatively impacting the mechanical properties of the weld.
Additionally, wrong grain form can result in uneven stress circulation. Identifying these usual flaws is vital for welders and examiners alike, as early discovery and modification are crucial to ensuring the long life and reliability of pipe systems.
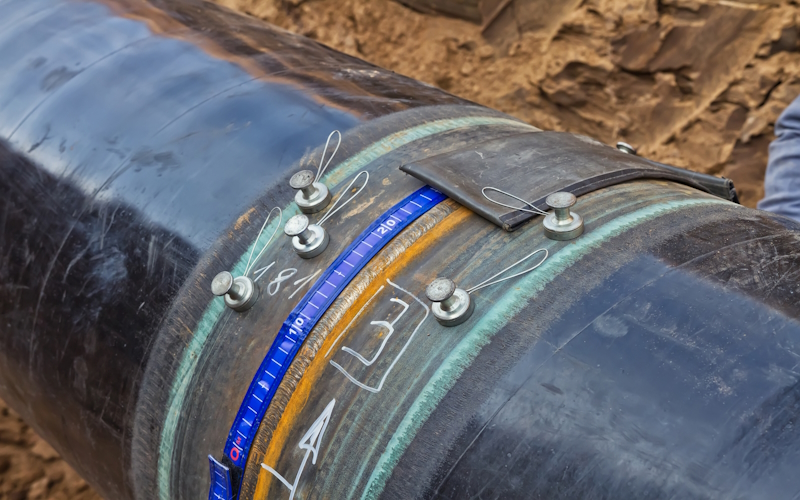
Products and Their Influence
Picking the suitable products for pipeline welding considerably influences the overall efficiency and reliability of advice the welded joints. The selection of base metals, filler materials, and coatings plays an important role in identifying the toughness, i loved this deterioration resistance, and sturdiness of the welds. For example, carbon steel is frequently utilized for its equilibrium of strength and cost, but it may be at risk to deterioration in certain environments, necessitating making use of protective finishings or corrosion-resistant alloys.
In addition, different steel welding needs mindful factor to consider of thermal development properties and potential galvanic corrosion. The compatibility of products can substantially influence the microstructure of the weld, bring about variants in mechanical residential properties. For instance, stainless steel provides outstanding corrosion resistance however might need certain filler materials to make certain an audio weld joint.
In enhancement, the impact of temperature and ecological problems on material option can not be taken too lightly. High-strength steels might lose ductility at raised temperature levels, while low-temperature applications may require products with improved toughness. Inevitably, understanding the implications of material choices is important for attaining ideal weld quality and protecting against failings in pipeline systems.

Governing Requirements and Compliance
Regulative requirements and compliance play a critical function in pipeline welding, establishing the framework within which safe and effective techniques are kept. These requirements are established by different organizations, including the American More about the author Culture of Mechanical Designers (ASME), the American Welding Culture (AWS), and the Pipeline and Hazardous Materials Safety And Security Management (PHMSA) Sticking to these guidelines guarantees that welding procedures meet the called for high quality and security benchmarks.
Conformity with governing requirements is important not only for making certain the honesty of the welds however also for shielding the setting and public security. Inspectors are entrusted with confirming that welding operations follow these requirements through strenuous evaluations of both the processes and the last welds. This involves assessing welder certifications, welding procedures, and the products used.
Failing to abide by established laws can lead to substantial effects, consisting of pricey fixings, lawful liabilities, and tragic failures. Consequently, organizations have to integrate conformity into their operational practices, cultivating a society of safety and high quality. Normal training and audits are vital parts in maintaining adherence to these regulative standards, guaranteeing that all employees are well-informed and geared up to promote the highest degrees of pipe welding quality.
Final Thought
In verdict, a comprehensive understanding of pipe welding evaluation is vital for ensuring weld quality and avoiding failures. By using vital examination methods and acknowledging common welding flaws, assessors can efficiently examine the stability of welds. Consideration of material choice and adherence to governing standards better improve the integrity and security of pipe systems. Ultimately, these techniques add to the avoidance of leakages and tragic failings, emphasizing the essential importance of rigorous inspection processes in pipe construction and maintenance.
In the realm of pipe welding examination, the risks are unquestionably high, requiring an extensive understanding of fundamental concepts to make sure weld quality and mitigate failing risks (Pipeline Welding Inspection).The honesty of a pipe is basically dependent on the top quality of its welds, making weld top quality a crucial element in guaranteeing risk-free and effective operation.Numerous elements add to the quality of a weld, consisting of the choice of welding process, the skills of the welder, and the problems under which the welding is executed. Undercut is an additional issue that can lower the weld's cross-sectional location, leading to tension focus points, while slag inclusion occurs when non-metallic product becomes caught in the weld swimming pool, negatively influencing the mechanical homes of the weld
In conclusion, a detailed understanding of pipe welding evaluation is crucial for ensuring weld high quality and protecting against failures.
Comments on “Pipeline Welding Inspection: Important Actions for Reliable Pipeline Building And Construction”